Operations Management
Safety Capacity
Written by Andrew Goldman for Gaebler Ventures
Planning your work below full capacity will allow your company to be more flexible and responsive. This concept is known as safety capacity and is explained in this article.
The concept of safety capacity is used by many large businesses but is widely underused and misunderstood by small businesses.
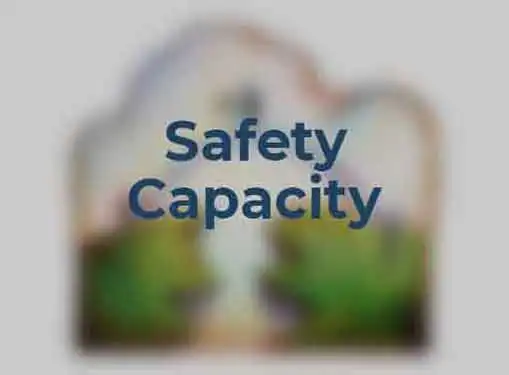
Safety capacity is the act of consistently planning your production below capacity. The reason for this is so the company can become more flexible to meet the changing needs of the customer. For example, if your company was operating at full capacity and your best customer needed extra product, you would be unable to meet their request. By allowing for safety capacity you company can become more flexible and more responsive.
One of the barriers to starting up a safety capacity program is the perceived cost of having employees on schedule for 40 hours of work, when they are only scheduled for 35 hours of work. It's important to distinguish between actual demand and actual production in this instance.
It is no good having your employees produce product for an extra ten hours just because they are there. This creates a situation where product is being produced that is not actually needed. This results in higher costs and higher inventories. These costs can easily outweigh the safety capacity time.
Once you've eliminated the unneeded production, you may have some weeks when you are overscheduled. Instead of using this extra time to manufacture unnecessary inventory, you can use this time to cross-train employees, have training courses, perform maintenance or clean up your facilities. If you are consistently over-staffed, it's time to review your actual demand and determine whether you are over-staffed to begin with.
When you switch to a safety capacity system, it's important to determine a number of hours that you will allocate to be the safety capacity. This depends on the nature of your business and your customers. If you have frequent last-minute requests or "off the cuff" orders, you would want to allow a greater amount of time than a company that has very consistent demand.
There are two main goals of the safety capacity system. The first is to create an environment that can better respond to the changing needs of the customer. By utilizing safety capacity you can become more responsive and flexible. In addition, if something should occur such as a late delivery or a machine failure, you will have some wiggle room built into your schedule.
A schedule that's fully loaded will have late deliveries to customers if a problem arises.
The second major goal of safety capacity, as discussed above, is to eliminate the habit of producing unnecessary inventory. It's extremely important that you do not have your employees produce product simply to keep them busy. If the product is being built for an anticipated order, that is okay, but if the product is just being built for inventory, it can probably be reduced or eliminated.
The costs associated with carrying inventory can be astronomical. The unneeded product takes up space in our warehouse, it runs the risk of damage or obsolescence and it requires employees to maintain it, count it and retrieve it.
By utilizing safety capacity, you can implore training during down times; reduce your inventories and costs while being more responsive and flexible in meeting your customers' needs.
Andrew Goldman is an Isenberg School of Management MBA student at the University of Massachusetts Amherst. He has extensive experience working with small businesses on a consulting basis.
Share this article
Additional Resources for Entrepreneurs
Conversation Board
What's your take on safety capacity?