Operations Management
Reducing Variance
Written by Andrew Goldman for Gaebler Ventures
If you have manual labor involved in your operation, there's a good chance you have a lot of variance in your process. Don't accept variance as part of the inevitable; seek to reduce variance to improve your quality.
Whether you are in a service or manufacturing industry, if manual labor is part of your operation, chances are you have a lot of variation in your process.
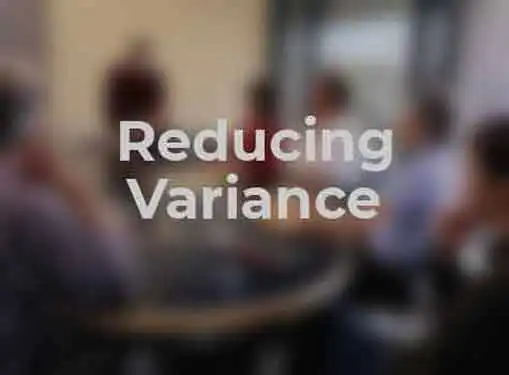
Variance is a tricky thing, especially with manual labor. Part of human nature is that not two humans are alike, as a result, we expect there to be variance when two different people are completing the same task.
While we should expect some variance, this does not mean that we cannot take measures to eliminate and reduce these variances. Variances are an enemy of quality control. We should seek to deliver a consistent product or service each and every time. As a result, variance cannot be complacently accepted, even if it is a part of human nature.
By standardizing our operations, we can greatly reduce variances. For example, the use of ruler or other measuring devices can improve our quality. If you have employees that cut or measure, make sure they have rulers and measuring cups. Colored visual signals can reduce variation and make the processes easier on the employee. By making the operation easier and standard for the employees, you'll improve your quality and reduce your variance.
I consulted for a company that packaged products in artful design. This required a lot of ribbon cutting and tying. Since there were several employees working in this area, one employees' ribbon looked different from another. To improve this, we first set out to standardize the ribbon cutting process.
Rulers and colored markers helped indicate where and how long a cut should be made. We also had a "demo" box placed in front of the employees so they could see the target goal. We worked with the packaging supervisor to detail the exact process that went into tying the ribbon. By duplicating the process and training the employees in the specific process, variance among packages was reduced significantly.
The above example brings about an interesting point. Standardize your process. If you can break down your process into specific standard steps, you can outline the process for others to duplicate. You yourself may not know the exact process, but your front-line employees will. Work with your employees to document the process. This will help with new employees and to identify discrepancies among employees. You'll be amazed how much can go into a seemingly simple operation. Once the process is broken down, however, it will be a lot easier to document and repeat.
Another key to reducing variance is to use better tools if they are available. This is not always practical, but the concept should be constantly on our mind. Often times our operation has been done elsewhere and there are tools available to make the job easier. Sometimes we've never heard of these tools and other times they seem too expensive.
Before deeming a tool too expensive, make sure you're basing this decision on numbers. See what the increased throughput would be and factor in the cost of reduced variation and defects. Keep a constant eye out for new tools that may aid an operation. I witnessed one operation where employees would painstakingly peel labels off a roll. With a few phone calls and an internet search, we had a label machine that allowed employees to pull the ribbon roll and the label would automatically come off the sheet. This simple tool made things a lot easier and greatly reduced the cost of the operation.
Variance indicates poor quality and it needs to be eliminated from your operation. Many operations that have high levels of variances chalk it up to the human factor. While human manual labor operations will result in some variance, there are measures you can take to eliminate these variances. Don't accept variances as part of your operation, seek to eliminate them and standardize your process whenever and wherever possible.
Andrew Goldman is an Isenberg School of Management MBA student at the University of Massachusetts Amherst. He has extensive experience working with small businesses on a consulting basis.
Share this article
Additional Resources for Entrepreneurs
Conversation Board
We welcome your feedback and questions regarding reducing variance in your business operations.