Operations Management
Receipt of Goods
Written by Andrew Goldman for Gaebler Ventures
How effectively your company receives shipments can have a major effect on your bottom line. Make sure your receiving procedures are in place and allow for a smooth receiving process.
How efficiently your company receives its raw materials can have a major effect on your costs.
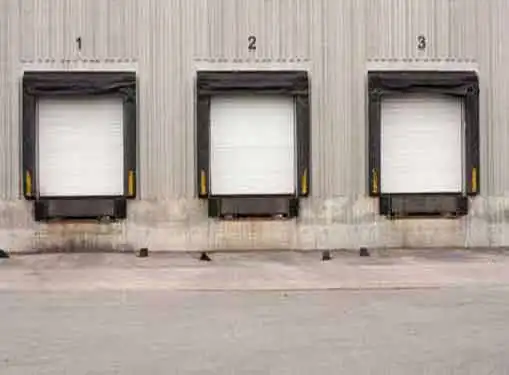
Too often small businesses consider the order complete once they receive a confirmation number. In effect, this is just the beginning. You may have saved money on the purchase, but if your receiving function is not operating efficiently, you may be giving that money right back.
The first step is to create a receiving schedule. Depending upon the size and nature of your business you may or may not have an individual receiving manager. In either case you should have someone who is in charge of receiving goods.
By creating a receiving schedule you are creating a communication bridge between the purchasing department and the receiving department. By using this calendar the receiving manager can know exactly what to expect and when to expect it. If there is a range of days where the product may arrive, this should be noted on the calendar. If the supplier calls with changes to the delivery schedule, the calendar should be updated so the receiving manager is aware of the issue.
Your receiving manager should use the calendar as a schedule for work. By knowing when goods are arriving your receiving manager can make sure that space is allocated in the warehouse and that loading dock is available. If there is clutter in the parking lot or at the receiving bay, the receiving manger can be proactive in clearing space for the expected delivery. The receiving manager can also use the calendar to communicate back to the purchasing department if goods have not arrived as promised.
Make sure you have a receiving process in place. This process should include paperwork and inspection upon receipt. Your receiving manager should be trained to deliver the bill of receipt to accounting or other necessary parties. Too often I see small businesses that let bills of receipt pile up and these result in confusion and lost paperwork. In my consulting experience I've seen companies scramble around for material because the supplier says the product was delivered but the whereabouts in the warehouse are unknown. Your receiving manager should also keep a log on what was received and where he put the material. By completing this log, the receiving manager can accurately communicate with the production team if there is a question on material receipt and location.
Establish an inspection routine as well. This inspection could be a sample of received product or a verification of the entire shipment. The quality of product as well as the number of products delivered should be verified.
Remember, this inspection process is costly and technically not a value added activity. This emphasizes the need to have reliable suppliers. If you have a good working relationship with your suppliers, you may be able to spend less time on inspection.
The cost savings from using a reliable supplier can easily outweigh the cost-savings from a cheaper supplier.
Andrew Goldman is an Isenberg School of Management MBA student at the University of Massachusetts Amherst. He has extensive experience working with small businesses on a consulting basis.
Share this article
Additional Resources for Entrepreneurs
Conversation Board
Do you have structured processes in place for receiving goods at your shop? How's that going for you?