Resources When Starting a Business
Operations Management Issues in a Small Business
Written by Samuel Muriithi for Gaebler Ventures
Operations management has to do with the small business' creation of value added products in accordance to strict quality control measures and subsequent inventory management. The small business owner has to ensure that the right raw materials are purchased and that the intended products are produced efficiently and effectively. Issues of maintenance also arise here.
Production as an aspect of operations management is that process by which materials are converted to more useful forms.
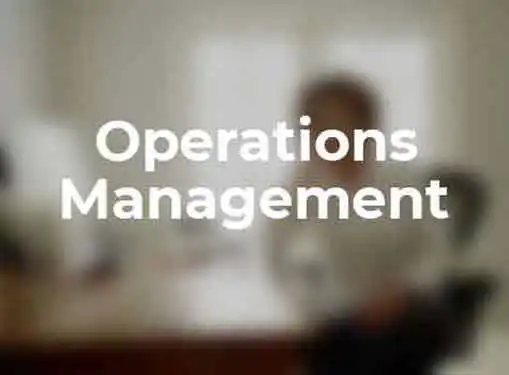
There are three types of materials i.e. raw materials, semi-processed/semi-finished goods, and finished products. In operations management there are four basic elements of production including machinery, equipment, methods and processes.
The same operations management concepts hold for both small and large scale production. Efficient and economical production must take into account a series of processes including purchasing, receiving, quality control, shipping, research and development, maintenance and inventory management.
The purchasing aspect is also referred to as procurement. It covers the aspects involved in obtaining all the elements required to make the production process a success. These elements include raw materials, equipment, machinery, components, supplies and all allied services. In preparing for purchasing operations the entrepreneur will need to know exactly what is required so as to make appropriate orders. He/she must know the best suppliers for these requirements and should have obtained price quotations and terms from the same. These requirements must be ordered and delivered on time and subsequently be managed as inventory.
The quality control aspect of operations management is all about ensuring that whatever products or services are produced the consumers requirements will be met or exceeded. Quality assurance methods cover all aspects of production starting from design and development, to production and installation, and to servicing and documentation. Standards must be upheld with respect to the raw materials used, production techniques employed, and the quality of the final product.
The concept of lean manufacturing is also ingrained in optimal operations management whereby focus is placed on minimizing the seven types of conventional manufacturing wastages. These are over-production, waiting time, transportation, processing, inventory, motion and scrap. The elimination of these wastages precipitates the improvement of quality, the reduction of production time, and the overall reduction of production costs.
Appropriate operations management techniques also influence optimal inventory management and the entrepreneur can adopt either of two techniques here. The JIT (just in time) technique aims to optimize returns on investment through a reduction of in-process inventory and allied expenses. The EOQ (economic order quantity) model seeks to identify the optimal quantity to be ordered so that the sum of variable costs needed to procure and hold inventory is kept at a minimum.
Samuel Muriithi is a business owner in Nairobi, Kenya. He has extensive international business experience in the United States and India.
Share this article
Additional Resources for Entrepreneurs
Conversation Board
We greatly appreciate any advice you can provide on this topic. Please contribute your insights on this topic so others can benefit.