Operations Management
Mistake-Proof Your Operation
Written by Andrew Goldman for Gaebler Ventures
By mistake-proofing your Operation you can make it difficult for defects to get passed on to the customer. With reduced defects you'll find your quality and customer service levels both increasing.
The concept of mistake-proofing operations is common in the field of Operations Management.
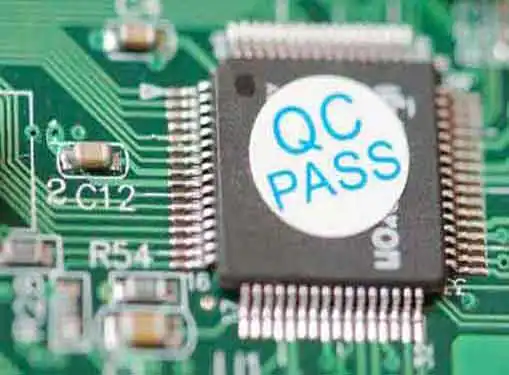
Mistake-proofing is generally defined as a process, where certain defects have been defined and prevented.
Once a process is mistake-proofed for a certain defect, it is impossible for that defect to occur and move on to the next station. For example, if you had an assembly line of hamburgers, and you had buns that were too small (defect) small cut out circles on the conveyor belt could be a mistake-proof spot. As buns that were too small in size passed over the hole, they would fall through. The holes effectively mistake-proof your operation and prevent small buns from passing on to the next stage of your operation.
There are many advantages to mistake-proofing your operation. Defects will be greatly reduced, your process will become more efficient and quality control is made easier.
Think about the aforementioned hamburger example. Instead of having inspectors taking time to inspect the buns, the process is self-sustaining and the quality control is completed automatically. In addition, inspections and sample sizes are not fool-proof; therefore defective buns can slip past them and make it to next station or ultimately the final customer.
Finding areas to mistake-proof your operation can be challenging. The process starts with the identification of a recurring defect.
Once the defect has been located, you can take measures to start improving the process. If you know an area where a defect is occurring, you should starting taking action immediately. That area should be red flagged and you and your employees should begin brainstorming possible solutions and prevention techniques.
It is crucial that you involve your employees in this process. They are the ones working on the front lines and they will have invaluable ideas regarding the process.
Any idea that will start immediately helping the problem should be put into place. This may mean additional inspection time or measuring techniques (scales, rulers etc). These methods are costly and time -consuming.
From this point you will want to develop a fool-proof system that can be incorporated into your process without much time or leg work. This can be difficult and may take time. Again, the more people you have involved in the brainstorming session the better.
Mistake-proofing techniques can be used to solve problems anywhere in your business. If you've identified a problem where customer service reps are continually missing information on sales invoices, try and find mistake proof techniques to solve the problem. Maybe the sales invoice won't save on the computer until all of the necessary data is complete. Or, a less expensive option of reorganizing the sales' invoice, so all of the pertinent information is in the same section.
You should develop a company culture that targets problem areas throughout your company. You'll find certain problems repeat themselves, and these are great areas to implement mistake-proofing techniques.
Get creative and involve all of your employees. By solving problems and putting the solution into the process, you'll find quality and productivity both increasing dramatically.
Andrew Goldman is an Isenberg School of Management MBA student at the University of Massachusetts Amherst. He has extensive experience working with small businesses on a consulting basis.
Share this article
Additional Resources for Entrepreneurs
Conversation Board
Does your organize put up with mistakes or do you identify them and eliminate them?