Operations Management
Kanbans
Written by Andrew Goldman for Gaebler Ventures
Kanbans are an incredible tool used in Operations Management. Learn how this simple visual system can help your company.
Kanban is the Japanese word for sign.
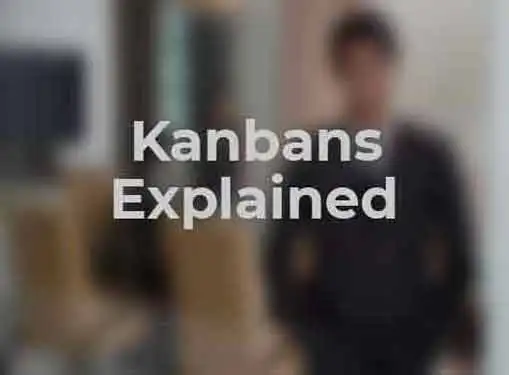
In Operations Management, it is a term used to describe a visual reorder system. Kanbans are simple to use and can be utilized to greatly improve your Operations while reducing your inventory. In addition, Kanbans can help improve your throughput while eliminating inventory shortages.
There are many applications of Kanbans. For the purpose of this article, I will use a couple of examples and how they can be applied to small businesses. One method of Kanbans is called the Two-bin system. With a two-bin system, your production team draws inventory from one bin while the other bin contains enough inventory to cover production until the first bin can be refilled.
For example, if you manufacture portable grills, your employees may have one part of the operation where they screw handles onto the grill top. In order for the employees to operate smoothly, they should have a container with the handles.
Rather than having large amounts of handle inventory clogging up the floor, the employees would have one bin containing X number of days or hours supply. When the employees would run out of handles in the first bin there would be a purchase card at the bottom of the bin. This card would go to the purchasing department to alert them to order more handles. While the team waits for the new order to arrive, they use the second bin, which should contain enough handles for the production team during the order lead time.
It's important to note that the card at the bottom of the first bin could go to the purchasing department to place an order or another section of the company that stores the handles. You could also utilize a one-bin system, where the handle container (or shelf) would have a visual line or color to indicate when to reorder. In this instance, the handles below the reorder line would be enough to cover the production team until a new order would arrive.
The second method of Kanban that I will discuss is a card replenishment system. With the card replenishment system, when a product or material is used up, a card attached to that material is placed in a container. The card attached to the material will have the amount and the specific type of material written down.
At the end of the day, the purchasing department retrieves the container with the cards and makes orders according to what was used up in that given day.
With this example, the card indicates that the material has been used up. The card should be located at the point where there is only enough inventory to cover the company during the purchasing lead time. For example, if you manufacture flashlights your light-bulbs may be stored in a warehouse. Let's say you use light bulbs at a rate of 1000/week and it takes 3 weeks to receive new light bulbs. You would want a safety inventory of 3000 light bulbs. Once your employees used up the last box before the safety inventory, they would bring the attached Kanban card to the purchasing department. This card is a trigger for the purchasing department to order new light bulbs. In the meantime, the employees will have the last box plus the safety stock of 3000 light bulbs.
There is a lot of literature and examples of Kanban usage. The concept is simple but its uses are widespread. Learn more about Kanbans and apply them to your operation to gain productivity and efficiency.
Andrew Goldman is an Isenberg School of Management MBA student at the University of Massachusetts Amherst. He has extensive experience working with small businesses on a consulting basis.
Share this article
Additional Resources for Entrepreneurs
Conversation Board
What's your take on kanbans? We welcome all comments and questions.