Operations Management
Eliminating Bottlenecks
Written by Andrew Goldman for Gaebler Ventures
Our operation is only as fast as our slowest process. To be successful, we need to target and eliminate bottlenecks.
In general, a bottleneck is a process in an operation where the capacity is less than demand placed upon that operation.
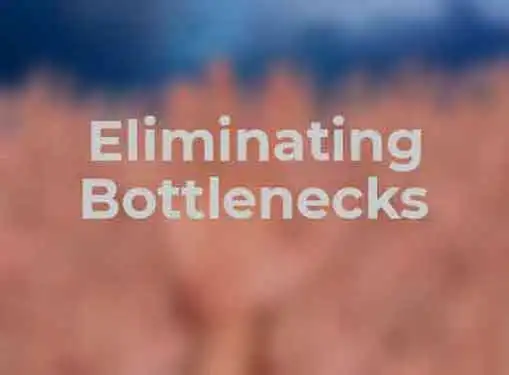
We are all somewhat familiar with the term, and in many cases, we know exactly where the bottlenecks are in our own operation. It is important to understand bottlenecks and the concept of 'throughput' if we are to maximize our efficiency and reduce the negative effects that bottlenecks can place on our operation.
First and foremost, understand that you entire process is only as fast as your bottlenecked operation. For example, if you produce bottled water, the bottling, labeling and boxing of the product could all be done at 100 bottles/minute, but if your capping machine can only do 10 bottles/minute, your entire production operation will only produce 10 bottles/minute. Clearly, if you can increase the throughput of the bottleneck, your entire throughput will increase. This simple example stresses the importance of zeroing in our bottlenecks and trying to improve these processes.
Bottlenecks can be extremely frustrating. Sometimes they are unavoidable, and restricted by the performance of a particular demand or geographical setting. Despite this, there are still ways to help out the bottleneck and improve your operation. You want to make sure that your bottlenecked operation is running as much as possible. This may mean staggering lunch breaks so an employee keeps your bottlenecked operation operating. Your bottlenecked operation should never stop, keep it running during coffee breaks and lunch breaks.
Since your total throughput can never exceed your bottleneck's pace, try and balance your operations with the bottleneck. Although this won't increase your throughput, it will reduce work-in-process and long queues before the bottleneck. These queues can create problems of their own and tend to clutter our workspace. By balancing your operations you can better manage your production due to the elimination of unneeded product.
When you have a bottleneck in your operation, it's crucial that the overloaded operation never stops or breaks down. If it is a piece of equipment, make sure that you have solid preventative maintenance program in place. You definitely don't want your bottlenecked machines breaking down and causing further chaos. It is important to have preventative maintenance for all of your machines, but keep a real close eye on your overloaded equipment.
If your bottleneck is not a piece of equipment, you may have an opportunity to eliminate or improve the overloaded area. Get creative in increasing the throughput, an additional employee or a new tool may increase the throughput of the operation. If you've identified a bottleneck in your operation, an improvement will lead to an improvement in the throughput of your entire process, so it's definitely worth the effort. You should feel comfortable cross-training and juggling employees around to balance your operation.
Andrew Goldman is an Isenberg School of Management MBA student at the University of Massachusetts Amherst. He has extensive experience working with small businesses on a consulting basis.
Share this article
Additional Resources for Entrepreneurs
Conversation Board
Have you run into bottleneck issues? How have you solved them?