Operations Management
Capacity Planning
Written by Andrew Goldman for Gaebler Ventures
The capacity of your company to meet expected demand should be measured in both the short-term and the long-term. Properly managed capacity can have great benefits for the small business.
Capacity planning is the analysis of what you are capable of producing versus what your expected demand will be.
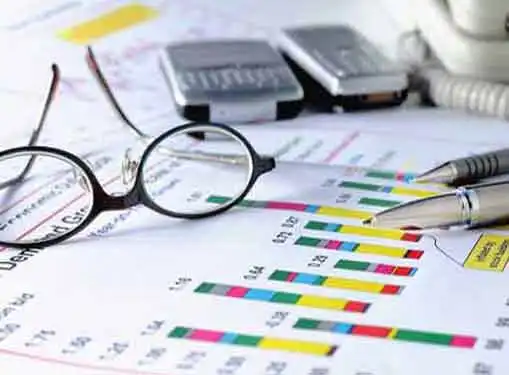
Capacity planning should take place at multiple levels. In order to increase capacity, you may have to purchase new equipment or change facilities. This can be a lengthy process. As a result, capacity planning needs to be analyzed in the long-term.
In addition, on a monthly basis a production report is generated, demonstrating expected future demand and the production necessary to meet that demand. The capacity of the business needs to be checked versus the production plan in order to ensure an achievable plan. If there is not enough capacity, you may have to run an extra shift, use overtime or subcontract work.
In the short-term when the Master Production Schedule is generated, capacity planning needs to be used to balance the workload. Are the machines running full-capacity on Monday but less than half-capacity on Friday? In the short-term you want to manage capacity to balance the workload, ensuring an even flow of work.
Capacity should be first be analyzed during business planning sessions. The company should have a good sense of their current capacity and at what percentage they are operating. This number can be tricky, if you're running close to full-capacity but most of your product goes to inventory, then you might be okay. You should measure your capacity versus actual demand, not versus actual production. During these business planning sessions, the long-term should be analyzed and discussions regarding the purchase of equipment or facilities should be discussed. These are obviously major decisions with huge capital expenditures. As a result you will want to analyze your options fully with financial data.
In the medium-term, capacity should be analyzed during monthly meetings. If capacity is consistently less than what is demanded, it may be necessary to take short-term measures. When making the decision to increase capacity in the medium-term financial data and comparisons need to be completed. The decision to hire more people, subcontract or use overtime are all costly and need to be analyzed appropriately.
In the short-term, capacity should be analyzed on a weekly basis when the production schedule is being released. You want to have a balanced workload if possible. You should fully understand where your bottlenecked machines are and manage the throughput as close to the bottleneck as possible. There's no point pumping out product through certain machines only to have them form a queue at your bottleneck.
The decision to increase capacity is not easy and can be extremely costly.
Make sure you've fully analyzed all of your options and backed them with financial calculations.
If you do purchase a new piece of equipment, there's a tendency to want to operate them at full-capacity to reduce the return on investment. This is a false way of thinking. You should be operating to meet your demand, not to keep the machines running. This line of thinking will lead to excess materials and increased costs.
Andrew Goldman is an Isenberg School of Management MBA student at the University of Massachusetts Amherst. He has extensive experience working with small businesses on a consulting basis.
Share this article
Additional Resources for Entrepreneurs
Conversation Board
Questions? Comments? Suggestions? Share your thoughts on capacity planning.